Business Content
From A to Z: 26 Inventory Terms
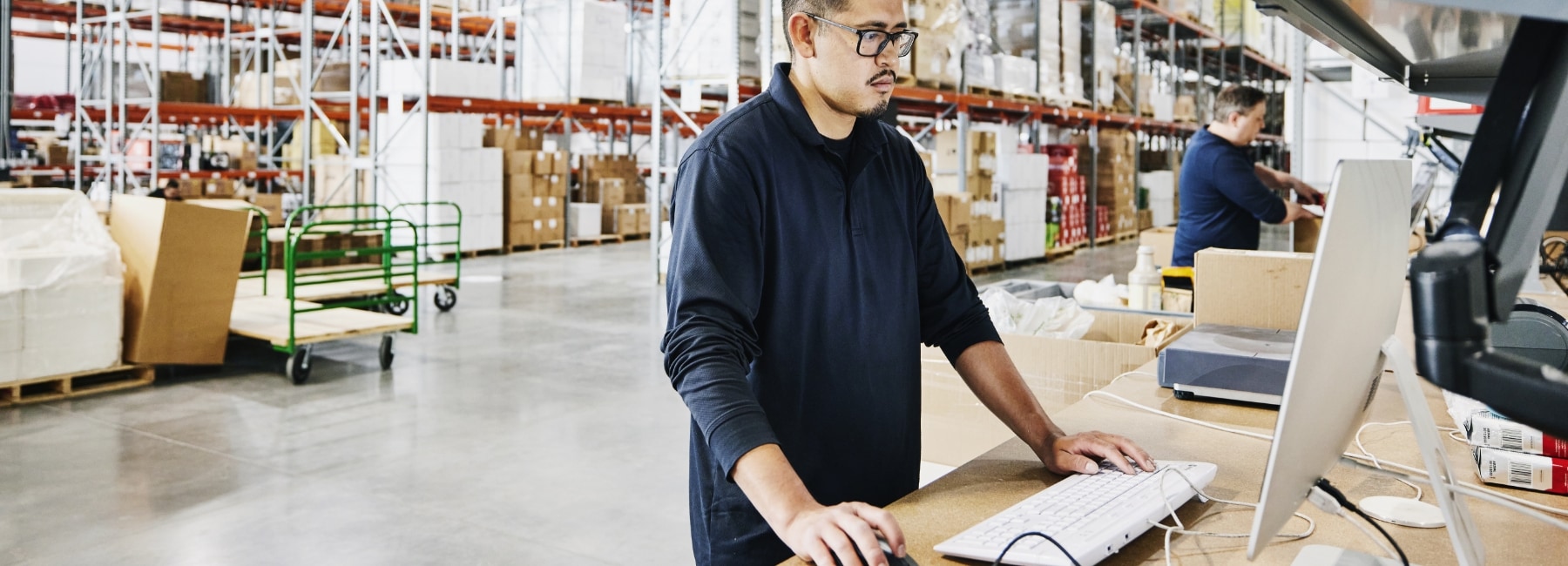
The world of inventory management is full of specialized jargon and easily confused abbreviations.
Here, we’ll demystify 26 tricky inventory terms you’re likely to encounter as a small-business owner:
FIFO assumes that the oldest inventory is sold first.
- Age Management
Monitoring the age of inventory items to ensure that they are sold or used before they become obsolete or outdated.
- Backflush
A process of recording the use of raw materials after production is completed, to simplify and streamline the accounting process.
- Batch Picking
The process of picking multiple orders at the same time, by grouping together items that are needed for different orders.
- Blind Count
A physical inventory count in which the counters do not have access to the inventory records or counts, to ensure that the count is accurate and unbiased.
- Carrying Cost
The cost of holding and storing inventory, including rent, utilities, insurance, and other expenses associated with holding inventory.
- Chargeback
A reversal of a credit card transaction that occurs when a customer disputes a charge on their credit card statement. Chargebacks can occur, for example, when a customer returns a defective or incorrect product.
- Cycle Counting
Regularly counting a portion of the inventory, rather than conducting a full inventory count, to ensure accuracy and identify issues before they become significant.
- Deadstock Management
The process of managing and disposing of inventory items that are no longer useful or have become obsolete.
- Ending Inventory
The total value of inventory on hand at the end of a reporting period.
- FIFO/LIFO (First In First Out/Last In First Out)Two inventory accounting methods used to determine the value of inventory sold and the cost of goods sold. FIFO assumes that the oldest inventory is sold first, while LIFO assumes that the most recently acquired inventory is sold first.
- Gross Margin
The difference between revenue and the cost of goods sold, expressed as a percentage.
- Initial Markup
The difference between the cost of a product and its selling price, expressed as a percentage.
- Inventory Control
The process of managing and optimizing a company’s inventory levels and associated costs.
- Landed Cost
The total cost of a product, including its original cost, transportation, customs, taxes, and other fees incurred until it is received in inventory.
- Lights Out
A fully automated warehouse or distribution center where little to no human intervention is needed for daily operations.
- Order Hold Time
The amount of time an order is placed on hold before being fulfilled or canceled.
- Purchasing Procedure
The set of steps and policies a company follows to acquire goods and services from suppliers.
- Reorder Points
The predetermined inventory levels at which a company will need to reorder or replenish stock. These points are based on factors such as lead time and demand variability.
- Sell-Through
The rate at which inventory is sold to customers over a specified period of time, typically expressed as a percentage of inventory available.
- SKU (Stock Keeping Unit)
A unique identifier assigned to each item in a company’s inventory. SKUs enable companies to track sales, inventory levels, and other important metrics.
- Stock-Out Management
The process of minimizing the impact of out-of-stock situations by quickly replenishing inventory or offering substitutes.
- Stocktake Policies
The set of procedures and practices used to conduct physical inventory counts.
- Supply Chain Management
The process of planning, executing, and controlling the flow of goods and services from suppliers to customers.
- Turnover
The rate at which inventory is sold and replaced over a specified period of time.
- Velocity Reports
Reports that provide detailed information about the movement of inventory through a company’s supply chain.
- Zone Picking
A method of order fulfillment in which workers are assigned specific zones within a warehouse or distribution center and are responsible for picking all items within their assigned zone.
Defining Success
If you’re ready to put your knowledge into action, consult your financial institution.